La costura de soldadura de dos tuberías es la sección menos confiable de las tuberías. La duración de la línea depende de su calidad. Para evitar accidentes durante la operación de la estructura, se lleva a cabo la detección de fallas en las tuberías. Esto es especialmente importante para las carreteras ubicadas bajo tierra.
Información general
Existen varios métodos para detectar defectos en soldaduras de tuberías:
- magnético;
- acústica;
- eléctrico;
- óptica.
Su tarea es determinar la estanqueidad de las uniones, la resistencia del metal en las costuras, si hay tensiones y otros parámetros que determinan la confiabilidad de las tuberías. Al mismo tiempo, los métodos de detección de fallas son casi los mismos para todos los tipos de redes: calefacción, gas, agua, oleoductos.
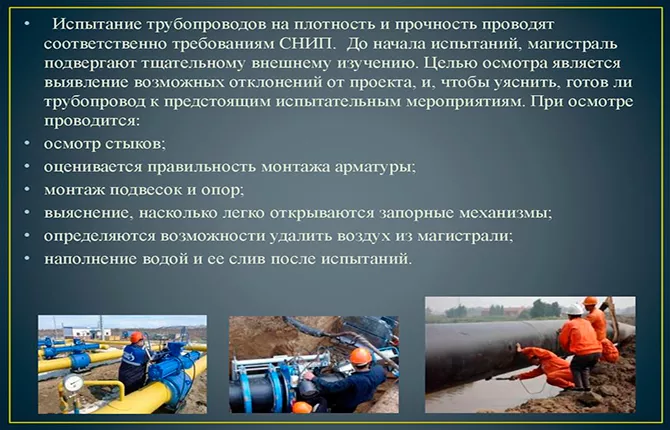
Todos los métodos mencionados anteriormente pertenecen a la categoría de tecnologías "no destructivas" . Es decir, la detección de fallas se lleva a cabo directamente en el sitio de construcción. Las uniones de tuberías no se destruyen, lo que reduce el costo del trabajo de instalación.
La detección de fallas en tuberías se basa en un escáner llamado detector de fallas. Cada tecnología tiene su propio principio de funcionamiento de este equipo. Detectores de fallas más eficientes:
- corriente de Foucault;
- ultrasonidos;
- polvo magnético;
- capilar.
Detalles sobre métodos
La detección de fallas en tuberías es un procedimiento que debe realizarse después de la instalación de la tubería. Esto evitará su posible destrucción durante el funcionamiento. La detección de fallas permite detectar cualquier defecto en las tuberías. El principio de funcionamiento de los escáneres que se utilizan en el proceso de diagnóstico es diferente. Por lo tanto, vale la pena estudiar primero cada uno de ellos con más detalle.
Detectores de defectos por corrientes de Foucault
El principio de funcionamiento del dispositivo se basa en la creación de corrientes de Foucault que se dirigen desde el plano exterior de la tubería hacia el interior a través de la soldadura. La corriente que pasa a través de una estructura metálica homogénea no cambia sus parámetros. Si hay defectos dentro de la costura, es decir, se rompe su uniformidad, la resistencia aumenta, lo que reduce la fuerza de la corriente de Foucault.
El detector de fallas corrige y descifra esta disminución, determinando la calidad del metal de soldadura, defectos y heterogeneidad.
Ventajas del método:
- alta velocidad de trabajo;
- error de resultado bajo;
- bajo costo de operaciones.
Contras:
- espesor de la costura examinada - no más de 2 mm;
- la confiabilidad del dispositivo es baja.
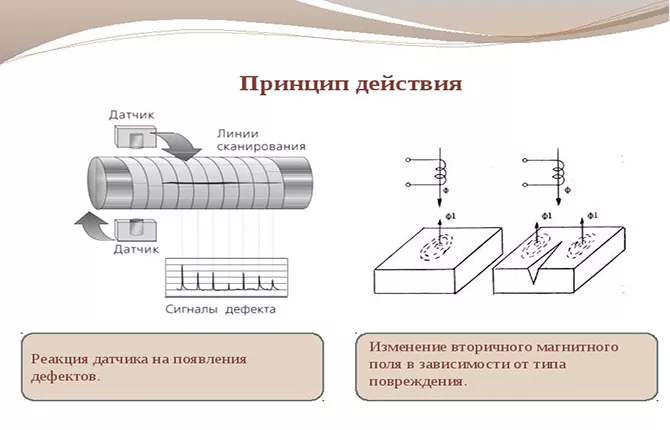
Detectores ultrasónicos de fallas
La prueba ultrasónica de tuberías se considera la tecnología más utilizada. Se lleva a cabo utilizando cinco métodos diferentes para la detección de defectos:
- Método de eco de pulso.
- Sombra.
- Espejo de eco.
- Espejo-sombra.
- Método delta.
En el primer caso, el ultrasonido es enviado por el instrumento a través de la capa de soldadura. Si hay defectos en el interior del metal, el pulso se refleja en forma de eco. Es decir, el ultrasonido regresa. El dispositivo registra el tiempo de retorno, que determina la profundidad de la cáscara o poro.
En el segundo caso, no solo se utiliza un dispositivo que envía una señal ultrasónica, sino también un reflector. Este último se instala en el lado opuesto de la unión soldada de la tubería. Si se conoce la distancia entre las dos partes del dispositivo y el tiempo de propagación del sonido, al cambiar el segundo parámetro (aumento) es posible determinar dónde se encuentra el defecto, qué tamaño tiene.
La tercera versión de la detección ultrasónica de fallas se parece a la primera.Solo el detector de fallas se suministra con un reflector, que se instala en la superficie superior de la costura, así como un emisor de señal. Ambos elementos son paralelos entre sí. Si llegó una señal al receptor, significa que hay un defecto dentro del metal que reflejó el haz.
El siguiente método es similar al anterior. La diferencia es que el dispositivo de señalización y el reflector están ubicados en un ángulo de 90° entre sí.
El quinto método de detección ultrasónica de fallas rara vez se usa. Las razones son la complejidad de configurar el equipo, la larga decodificación de los resultados. Se basa en la redirección de la energía ultrasónica, cuya dirección cambia el defecto de la soldadura.
En este caso se suministra una viga transversal transformándose en una longitudinal. Parcialmente hay un reflejo de espejo. El reflector capta exactamente la señal longitudinal, cuya fuerza determina la magnitud del defecto en el acero.
Detectores de defectos por partículas magnéticas
Esta detección de fallas se basa en la propiedad del acero para cambiar el campo magnético cerca de áreas que difieren de la parte principal en baja densidad. Aquí se vuelve más débil. Las grietas, cavidades o poros en el interior del metal tienen una densidad baja debido al aire que contienen.
El polvo magnético, también conocido como sustancia ferromagnética, se utiliza para detectar defectos en las tuberías. Se vierte sobre la soldadura, donde se suministra corriente eléctrica con la ayuda de dos bobinas: magnetizante y adicional. La electricidad dentro del metal forma un campo magnético. Si hay defectos, se debilita alrededor de ellos. Esta es la razón por la que se atrae el polvo magnético.
Si, durante el examen, se acumula polvo en la superficie, esto indica una cosa: se encontró un defecto en la soldadura en esta área. La detección de fallas en línea de las tuberías principales se lleva a cabo de esta manera.
Hay dos opciones para la prueba: seca y húmeda. En el primer caso, se utiliza polvo magnético. En el segundo, la suspensión de este polvo es una solución acuosa.
Para que la calidad de la inspección realizada con la segunda opción sea alta, es necesario tratar adicionalmente la superficie en estudio con un material intermedio: aceite técnico, grasa y otros.
Las ventajas de la inspección por partículas magnéticas incluyen:
- resultado visual, visible sin dispositivos adicionales;
- precio bajo.
Defectos:
- pequeña profundidad de examen - hasta 1,5 mm;
- solo se puede utilizar en tuberías ensambladas con aleaciones ferromagnéticas;
- dificultad para desmagnetizar tuberías grandes.
Detectores de defectos capilares
Esta tecnología se utiliza para detectar pequeñas grietas superficiales que no son visibles a simple vista. Confirman que el metal en la unión de dos tramos de la tubería no es homogéneo.
El proceso de detección de fallas en tuberías se realiza de la siguiente manera:
- Se aplica una sustancia indicadora, un penetrante, a la soldadura. Tiende a penetrar en los defectos más pequeños bajo la acción de fuerzas capilares. De ahí el nombre del método.
- La superficie tratada se limpia de la sustancia aplicada, que ya ha penetrado profundamente en el metal.
- Sobre ella se aplica el revelador en forma de polvo blanco. Puede ser talco, óxido de magnesio u otra sustancia. Tiene una propiedad importante: la adsorción. Es decir, puede absorber otras sustancias.
- El revelador comienza a sacar el penetrante de las grietas, lo que forma un patrón de fallas en las uniones en la superficie del polvo blanco. Al mismo tiempo, el indicador es claramente visible en los rayos ultravioleta.
Este tipo de detección de fallas en tuberías generalmente se usa si es necesario detectar fallas en la superficie del metal en la unión. Para defectos profundos, es inútil. Y esto es un menos. La principal ventaja es la facilidad de implementación.
Resultados
Para verificar las juntas de las tuberías en las tuberías principales, no es necesario utilizar un método de detección de fallas. Cada sitio puede ser encuestado de una forma u otra. Al elegir el método óptimo, primero debe evaluar cómo le corresponde la articulación. Por ejemplo, el método capilar es adecuado para tuberías de agua, solo el método ultrasónico para tuberías de petróleo y gas.
La detección de fallas en tuberías es un procedimiento necesario que le permite evaluar la calidad de la tubería tendida para identificar todas las fallas posibles. Se lleva a cabo de varias maneras. Es mejor realizar el procedimiento en la etapa de instalación de la tubería, de modo que después de completar el trabajo no encuentre "sorpresas" desagradables en forma de fugas o roturas.
¿Qué método preferirías usar y por qué? Escribe en los comentarios. Comparta el artículo en las redes sociales y márquelo como favorito para no perder información útil.
También recomendamos ver videos seleccionados sobre nuestro tema.
Diagnóstico de la parte lineal de tuberías principales.
Cómo es el control por rayos X de soldaduras en producción.