En el caso de la soldadura con arco de argón del aluminio, el arco es más estable cuando el electrodo está en posición vertical y se mueve a lo largo de la unión (durante la soldadura de las juntas a tope). Se puede insertar una varilla aditiva desde la parte frontal o posterior del arco. Sin embargo, en la mayoría de los casos se utiliza el primer método. La colocación del quemador y la varilla para el aditivo en el proceso de soldadura de uniones rectas puede ser como sigue: soldadura a tope con un aditivo, brida, con una superposición con una penetración.
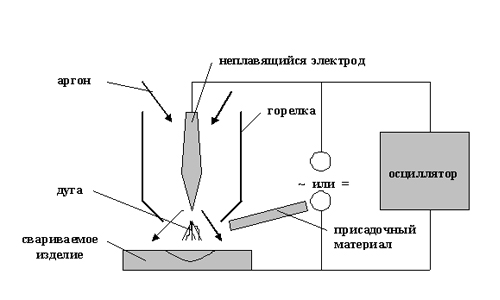
Esquema de soldadura de arco de argón.
En el caso de soldadura de la conexión abocinada, el arco debe ser de pequeña longitud, sin embargo, se deben evitar los cortocircuitos. Durante el proceso de soldadura, el electrodo se ubicará debajo de la parte superior de la brida. En el proceso de soldadura de costuras circulares, el eje del electrodo de tungsteno se coloca en un ángulo de 75-80 ° con respecto a la tangente con la base del producto en el sitio de soldadura, mientras que el producto deberá girarse a la misma velocidad. La costura circular termina con la superposición del comienzo de la costura en la sección con una longitud de 18-20 mm. Como resultado, el arco debería estallar. La rotación del producto debe acelerarse bruscamente. Si esta técnica se realiza correctamente, el cráter final será prácticamente invisible en la costura circular.
La soldadura debe realizarse a la máxima velocidad, por lo que, correctamente, un proceso de este tipo solo puede ser realizado por un soldador calificado. El movimiento del quemador debe ser directo, sin oscilaciones transversales. Si cumple con estas condiciones, puede obtener una suavidad y uniformidad a lo largo de toda la costura con una base lisa, brillante como un espejo en la parte superior y una fusión densa y uniforme en el lado incorrecto.
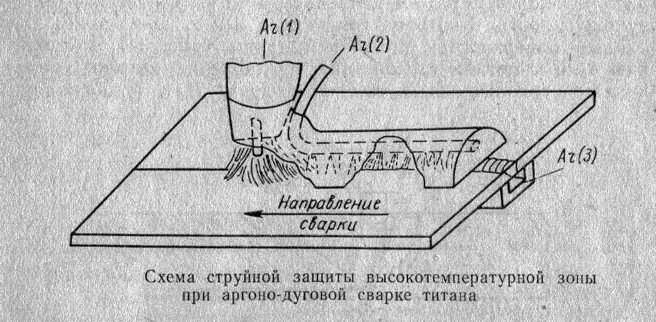
Esquema de protección de chorro durante la soldadura de argón-arco.
Artículos que serán necesarios:
- electrodo
- carcasa con aislamiento térmico;
- alambre para aditivo;
- forro
- varilla de carbono;
- dispositivo de soldadura
Asegúrese de ajustar el dispositivo de soldadura.
¿Cómo preparar la superficie para soldar?
En la mayoría de los casos, la base de las aleaciones de aluminio está cubierta con una película densa de pequeño espesor. Una película de este tipo tiene un alto punto de fusión y una gran gravedad específica. Dicho material complica la ignición y el mantenimiento del arco durante el proceso de soldadura, y también evita la conexión de los bordes del metal principal con el metal de relleno. Antes de producir la soldadura con arco de argón, tal película deberá retirarse de la base de los bordes unidos de las aleaciones de aluminio. La película puede ser removida mecánica o químicamente. El primero se utiliza en caso de producción individual. En el caso de la masa, es recomendable utilizar un método químico de limpieza de la base de aleaciones de aluminio.
El método mecánico de limpieza de la base de aleaciones de aluminio consiste en eliminar una capa delgada de metal con un cepillo de acero o papel de lija de pequeño espesor. El cepillo de acero debe estar hecho de alambre con un diámetro inferior a 0, 15 mm.
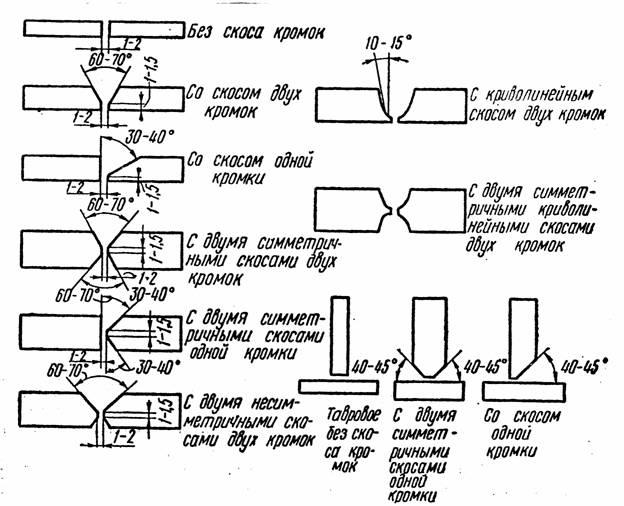
Tipos de preparación de cantos para soldadura.
Si utiliza un cable de gran grosor, sobre la base del aluminio, habrá grandes riesgos. En este caso, la capa de película se eliminará de forma desigual, lo que puede conllevar una calidad de soldadura deficiente.
Si limpia la base de aluminio con un cepillo de acero, puede obtener soldaduras aceptables. Antes de la limpieza, será necesario desengrasar la superficie, lo que se puede hacer con solventes.
La base de aleaciones de aluminio con zinc o magnesio se somete a una limpieza a fondo. La forma más fácil de limpiar las aleaciones de aluminio con cobre, hierro o manganeso es el silicio.
Tratamientos de superficie
Cabe señalar que la limpieza mecánica no puede garantizar la eliminación uniforme de la película de la base de las aleaciones de aluminio. Usar un cepillo es bastante difícil de limpiar los bordes que se unen. Por lo tanto, en lugares donde sea posible, será necesario mecanizar mecánicamente los bordes unidos en las máquinas. La efectividad del método de limpieza química se determina midiendo la resistencia de contacto, que es proporcional al espesor de la película. En este caso, se recomienda usar un microvoltímetro, graduado en micro-ohmios.
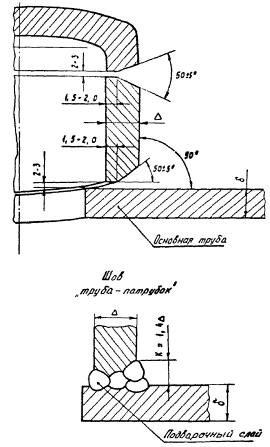
El esquema de la costura al soldar argón-arco.
Para las aleaciones de aluminio en la soldadura con arco de argón, puede utilizar los siguientes métodos de procesamiento químico:
- Desengrasado en solución alcalina y clarificación adicional en una solución de ácido fosfórico.
- Desengrasado en solución alcalina con mayor clarificación en una solución de ácido nítrico.
Los bordes de las piezas que se limpian mediante uno de los métodos anteriores se pueden soldar fácilmente. En este caso, las costuras tendrán una base limpia. Estos métodos de limpieza tienen la ventaja: en base a los bordes tratados, la película tendrá un ligero grosor durante 4-5 días.
Tipos de conexión existentes
En la soldadura al arco de argón de las aleaciones de aluminio, no hay flujo, por lo que en este caso no hay restricciones en la elección del tipo de juntas. Puede utilizar los siguientes compuestos:
- trasero
- quemado
- superposición
- articulación de vuelta ordinaria;
- junta de esquina
- Articulación en T
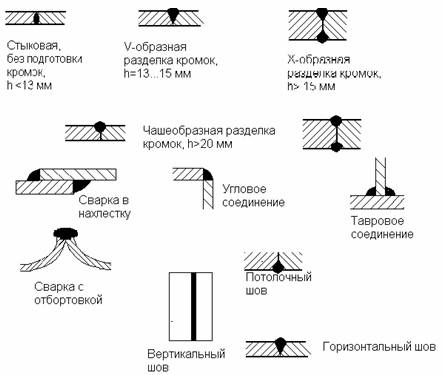
Tipos de uniones soldadas.
La soldadura a tope de láminas de aluminio con un grosor de 0, 8 a 3 mm se debe hacer con pequeños huecos. Cuando se suelda aluminio con un espesor de 1.5-3 mm, el espacio no debe ser más de 0.3 mm. La conexión abocinada se debe utilizar para materiales con un grosor de 0, 8-2 mm.
La soldadura con arco de superposición perforada se utiliza para materiales con un espesor inferior a 2 mm. Al unir este tipo de borde se debe presionar al forro. Esto es necesario para asegurar un ajuste perfecto de los elementos entre sí. La cantidad de superposición se determina según si planea fundirse a través de los bordes de la superposición o no. En el primer caso, el borde de la lámina inferior debe ubicarse en el extremo de la ranura de formación de modo que este borde se use para formar el lado inferior de la costura. La cantidad de superposición es igual al ancho de la ranura. Si es bueno quitar los bordes, puede hacer una conexión angular en el material con un grosor de hasta 2 mm sin el uso de material de relleno.
La ejecución de alta calidad de la conexión implica un ajuste preciso de los bordes. Debe saber que los huecos pueden provocar una mayor oxidación de los bordes, lo que conducirá a la porosidad y la aparición de zonas de fusión, que se ubican en el plano de contacto de los bordes con el aditivo instalado.
Matices para saber
Las aleaciones de aluminio tienen una alta conductividad térmica, por lo que el grosor de las piezas unidas debe ser el mismo en el sitio de soldadura. Si es necesario unir las piezas con paredes de diferente grosor, el borde más grueso debe cortarse en el sitio de soldadura hasta un espesor que sea igual al grosor del otro borde.
En los lugares donde el diseño lo permite, se recomienda utilizar revestimientos para facilitar el proceso de soldadura de aluminio con argón y para hacer grandes tolerancias en el ajuste de la junta. El revestimiento debe estar hecho de metal inoxidable. Se debe proporcionar una ranura en el forro debajo de la costura.
Las conexiones de tope bezkosnye se utilizan para aleaciones de aluminio con un grosor de menos de 3 mm. Si la pieza de trabajo es más gruesa, los bordes a soldar deberán ser cortados.
Las estructuras con un espesor de pared de 1-3 mm están conectadas por una junta de una sola capa. Si el grosor de la pared es superior a 3 mm, la unión a tope con bordes biselados debe soldarse en varias capas. La primera capa es fundir los bordes sin material de relleno, otra capa debe aplicarse con el material para el aditivo en la primera capa completada. Antes de colocar la segunda capa, la primera capa debe limpiarse por un método mecánico o químico. Cuando es posible soldar desde ambos lados, las piezas se sueldan sin bordes biselados de 6, 5 mm de espesor.
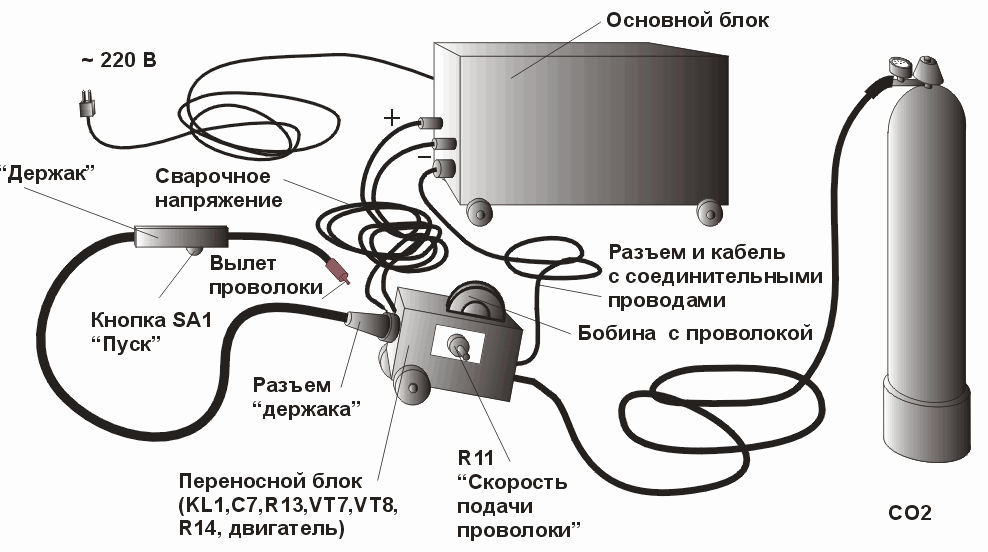
Esquema de la soldadora.
En el caso de soldadura de aluminio con un grosor de más de 1, 6 mm, deberá utilizar un cable de aditivo, ya que el baño fundido tiende a formar una base cóncava. Por lo tanto, no será posible utilizar la soldadura automática de aleaciones de aluminio si no hay un dispositivo para la alimentación mecánica de alambre para el aditivo. Asegúrese de estar configurado para este diseño.
Las juntas superpuestas y los vapores se sueldan al alambre como aditivo. Dicho cable no se puede usar, pero en este caso, el borde superior debe fundirse para poder reemplazar el cable por el aditivo.
Tecnología de soldadura de aluminio
Es bastante difícil encender un arco de corriente alterna al tocar una base de tungsteno hecha de aluminio con un electrodo. Para encender el arco, al comienzo de la costura de soldadura, debe colocar una barra de carbón, en la que se encenderá el arco. Después de calentar el electrodo de tungsteno, el arco puede ser fácilmente excitado en el metal principal. Encender el arco en la barra de carbón es bastante simple. El carbón tiene una conductividad térmica baja y, por lo tanto, en el proceso de un cortocircuito calentará rápidamente el material y el extremo del electrodo de tungsteno. El carbón y el tungsteno se pueden caracterizar por una poderosa emisión termiónica de su base, debido a la cual se excitará un arco estable durante la extracción del electrodo de tungsteno. El extremo caliente del electrodo de tungsteno emitirá una poderosa corriente de electrones que apoyan la combustión del arco en el proceso de transferencia al metal.
Si es necesario, la soldadura por arco en una base vertical se realiza de arriba a abajo para un espesor de metal de menos de 5 mm y de abajo a arriba para un espesor de pieza de trabajo de más de 5 mm.
En algunos casos, se pueden formar grietas al comienzo de la costura. Para evitar esto, deberá precalentar la unión en la parte inicial de la costura. Para hacer esto, en la longitud de 35-45 mm, el arco necesita calentar la unión varias veces, mientras que el arco debe arder en un gas inerte. Después de eso, la soldadura por arco se realiza a la velocidad máxima.
La elección del modo de soldadura está influenciada por la forma geométrica y las dimensiones de las piezas. Con la ayuda de la soldadura por arco en un entorno de gas inerte, se puede realizar la fundición de aluminio. Para evitar la aparición de grietas, las piezas fundidas deberán precalentarse a 400 ° C antes de soldar. La soldadura se realiza utilizando un metal para el aditivo, cuya composición corresponde a la composición de la fundición del metal. Los lugares sujetos a soldadura deberán ser pre-limpiados por medios mecánicos. Una vez hecha la preparación, la pieza debe colocarse en una carcasa con aislamiento térmico y luego enfriarse lentamente.
En el caso de un proceso de soldadura de aluminio mecanizado, deberá mantener una velocidad de alimentación de alambre específica para el aditivo. Si la soldadura por arco se realiza a la velocidad mínima, es importante evitar el sobrecalentamiento y la oxidación del alambre para el aditivo.
Dicho cable puede alimentarse de cualquier manera que garantice una velocidad de alimentación uniforme y su cambio. La soldadura con arco de argón mecanizado se realiza en el revestimiento. El uso de protección de gas desde el interior de la costura no dará resultados positivos.
La soldadura con arco de argón del aluminio es un proceso complejo, por lo que necesita conocer la tecnología de conexión.