Las tuberías son tuberías que consisten en una gran cantidad de tuberías, interconectadas por soldadura. Este último puede llevarse a cabo de manera deficiente, lo que conllevará consecuencias irreparables: una ruptura de la soldadura. Por lo tanto, antes de la transferencia de la tubería a la operación, se llevan a cabo pruebas no destructivas de las tuberías.
La importancia del control de calidad
Las estructuras principales de Tube están sujetas a fuertes cargas, tanto desde el interior como desde el exterior. Por ello, se presta especial atención al control de calidad de las soldaduras.
El proceso de soldadura está asociado a una alta temperatura, que funde el metal de las tuberías. Es en este momento cuando su estructura cambia. Si no sigue la técnica del proceso de soldadura, luego de enfriarse, se forman defectos dentro de la costura. El metal de soldadura se vuelve heterogéneo.
Tipos de defectos:
- Externo. Bien visible en la superficie de la costura. También se incluyen en esta categoría aquellos defectos que se encuentran en el interior del metal a una profundidad no mayor a 2 mm.
- Internas, también son profundas. Se encuentran a más de 2 mm de profundidad.
Los defectos en las juntas de las tuberías tienen diferentes formas y ubicaciones. Entre ellos hay fallas con nombres estándar y específicos:
- Grietas. Un defecto que es varias veces más largo que ancho. Este es el momento más peligroso de la soldadura, que a menudo conduce a su ruptura. Las grietas se dividen en dos categorías. Se pueden ubicar tanto dentro como fuera de la costura.A menudo hay grietas. Son los más peligrosos.
- Poros, son conchas. Defectos esféricos (la forma puede ser diferente, pero siempre hueca), formados debido a los gases que se liberan durante la soldadura del metal. Pertenecen al grupo interior.
- Cráteres. Estos son prácticamente poros que se han formado en la superficie de la soldadura de la tubería (pequeñas depresiones). El motivo de su aparición es una interrupción en el arco de soldadura. El peligro de los cráteres es que en su lugar de ocurrencia, el espesor de la soldadura disminuye. Y esto afecta la fuerza de la articulación.
- Rebajes. Formado en el borde de los extremos de los tubos y la soldadura. Esto reduce el área de contacto entre los dos metales. En tales secciones, la tensión interna aumenta, especialmente cuando aumenta la carga en la tubería.
- Afluencias. Esta es una capa de metal que se superpone a la superficie de la costura. Resulta que las capas superior e inferior prácticamente no están relacionadas. La sección transversal de la conexión no es la misma que requiere GOST.
- F alta de fusión. Tipo interno de defectos. Se caracteriza porque dentro de la conexión de la tubería hay un metal que no tiene las características requeridas. Fue creado bajo la acción de una temperatura más baja que la requerida por GOST. Por lo tanto, debido a las cargas en dicha sección, las tensiones del metal aumentan rápidamente, lo que conduce a la deformación con la ruptura posterior.
- El metal de soldadura es poroso. Estos son todos los mismos poros o capas, solo de tamaño pequeño y distribuidos uniformemente en todo el volumen de la unión soldada (en su conjunto o en secciones).
- Partículas extrañas dentro del metal de sutura. La razón es el mal trabajo del soldador. Antes de comenzar a soldar, todas las superficies a unir se limpian a fondo. Por lo general, se utilizan cepillos metálicos y desengrasantes para esto. Si no se lleva a cabo la preparación, entrarán residuos en la soldadura, lo que reducirá su resistencia.
- Grabar. Aquí es cuando la tecnología de soldadura se rompe y el arco del electrodo atraviesa el metal de la unión. Por la misma razón, se forma flacidez en el otro lado.
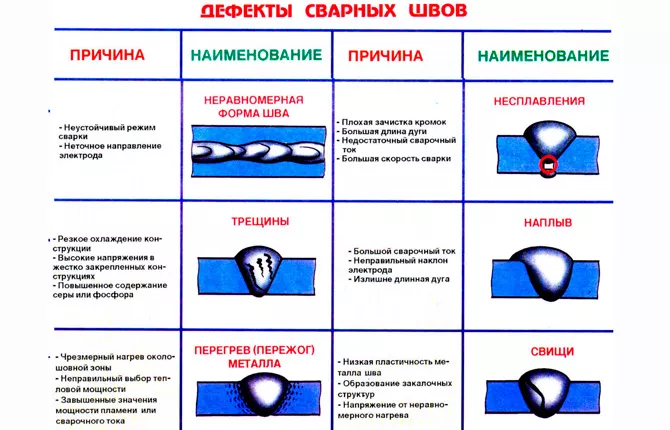
Para que todos estos problemas no afecten el funcionamiento de la tubería, se lleva a cabo el control. Hoy en día, se utilizan diferentes métodos, pero todos entran en la categoría de no destructivos. También existen métodos destructivos, pero se utilizan para investigaciones de laboratorio. No destructivo en todos los demás casos.
Son convenientes porque:
- no es necesario cortar el objeto de prueba y llevarlo al laboratorio;
- todos los procesos se realizan en el sitio de soldadura;
- Se requiere un equipo compacto y liviano para realizar las pruebas.
Existen requisitos estrictos para las pruebas no destructivas de la tubería. El diagnóstico lo realiza un especialista capacitado. Al mismo tiempo, se observan estrictamente las normas y reglamentos para realizar el control.
Qué métodos se utilizan durante las pruebas no destructivas
Existen varios tipos de ensayos no destructivos de tuberías, que utilizan diferentes materiales, dispositivos y tecnologías.
Básico:
- Control de medición visual.
- Detección de defectos radiográficos.
- Usando ultrasonido.
- Detección de defectos magnéticos.
- Método capilar.
Medición visual
Este tipo de inspección de tuberías se basa en la inspección de las juntas de las tuberías, tanto visualmente como con la ayuda de instrumentos de medición. Por lo tanto, esta técnica detecta solo defectos externos.
Este método no destructivo es inexacto, aunque fácil de implementar. Este tipo de control es obligatorio. Se lleva a cabo antes de pasar a otro método no destructivo. Después de todo, al encontrar un defecto en la superficie, no puede pasar a otra etapa, que es más costosa de realizar.Tal unión puede rechazarse inmediatamente.
En cuanto a la facilidad de conducción, generalmente se usa un dispositivo de medición simple para esto, por ejemplo, un calibrador o una regla. Antes de las mediciones, el área defectuosa se limpia con alcohol, ácido u otro solvente.
Si, por ejemplo, la grieta es pequeña, se toma una lupa para ayudar. Un requisito previo para este tipo de ensayo no destructivo es determinar la forma del defecto y su tamaño.
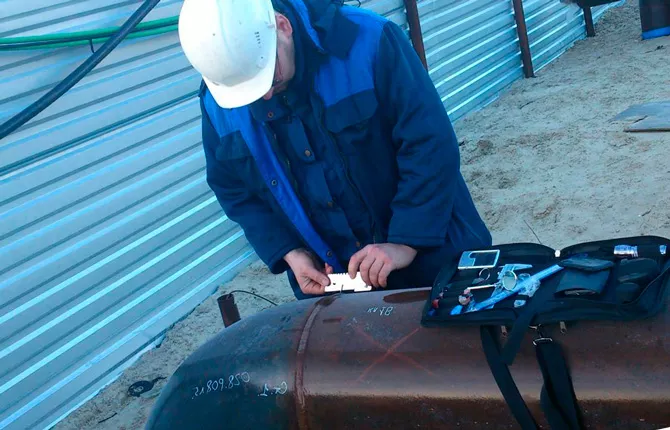
Detección de defectos radiográficos
Uno de los métodos más precisos de prueba no destructiva de la tubería, que le permite identificar incluso fallas menores en la soldadura. Al mismo tiempo, también se determina su ubicación exacta.
La técnica se basa en una radiografía convencional. Usan una pequeña instalación que brilla a través del metal de la conexión de los elementos de la tubería y los muestra en una película de rayos X.
Pruebas ultrasónicas no destructivas
La tecnología se basa en cambios acústicos en el interior del metal. Si es homogéneo, el sonido pasará sin cambiar sus características y dirección. Cuando se encuentre un defecto en el camino, aparecerán cambios y se reflejarán en el receptor. El parámetro principal del cambio es la velocidad del movimiento del sonido.
La esencia de la técnica no destructiva:
- El amplificador emite ultrasonido con una frecuencia de vibración ultra alta;
- pasa por la soldadura ;
- si choca, por ejemplo, con una grieta o un caparazón, se reflejará desde su superficie interna (cavidad), cambiará de dirección y regresará al receptor.
Cuanto mayor sea el ángulo de refracción, mayor será la grieta u otro defecto.
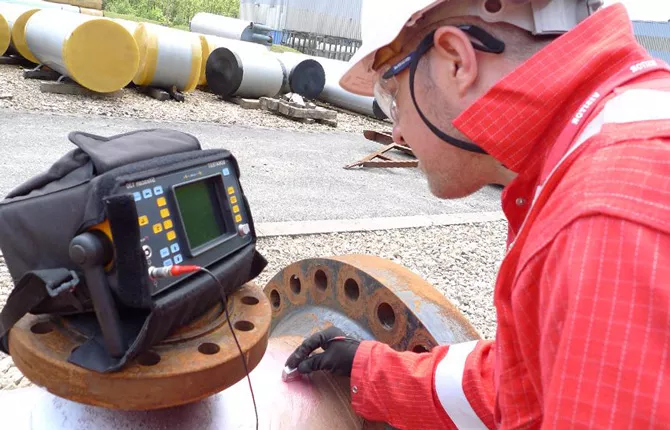
NDT magnético
Existe un término como permeabilidad magnética. Esto es cuando las ondas magnéticas atraviesan el metal durante un cierto período de tiempo. Si este indicador disminuye, entonces dentro del material en el camino las olas encontraron un obstáculo, que comenzaron a rodear. Por lo tanto, su velocidad disminuyó y su tiempo de viaje aumentó.
Se utiliza equipo especial para llevar a cabo esta prueba no destructiva de uniones soldadas en tuberías. Con su ayuda, las ondas electromagnéticas atraviesan el metal. El polvo se vierte preliminarmente sobre la superficie o se vierte una suspensión con hierro en el interior. El mineral se acumula alrededor del área defectuosa.
Hay otra opción llamada magnetografía. Aquí, en lugar de polvo o suspensión, se utiliza una película magnética. En él, se muestran todas las deficiencias del metal. Después de realizar los procedimientos de control, la película se coloca en un detector de fallas, desde donde se lee la información. Puede ser sonido o en forma de imagen.
Ensayos no destructivos capilares
Esta tecnología permite identificar defectos de soldadura en un sistema de tuberías utilizando fluidos especiales llamados penetrantes. Su principal propiedad es la de penetrar en los materiales, aunque tengan cambios capilares.
Tales líquidos incluyen:
- queroseno;
- aguarrás;
- benceno;
- aceite de transformador, etc.
Si el penetrante ha atravesado el metal de la unión de la tubería, significa que hay una falla en ella. Si no se aprueba, entonces todo está en orden.
Proceso NDT:
- Se aplica tiza o caolín en forma líquida a la unión soldada de la tubería;
- después de que se seque la capa aplicada, se retira la parte seca;
- Se aplica queroseno sobre la capa restante;
- en media hora tienes que comprobar el reverso de la unión;
- si se encuentran manchas de queroseno allí, entonces la costura está defectuosa, si no, la conexión es confiable.
Hoy en día, se agregan sustancias a los penetrantes que ayudan a identificar más claramente las deficiencias de los metales. Básicamente dos:
- pigmento rojo;
- sustancia luminiscente.
El primero se utiliza cuando el control se realiza durante el día con luz natural en el sitio. La segunda noche, para la que utilizan lámparas con luz ultravioleta.
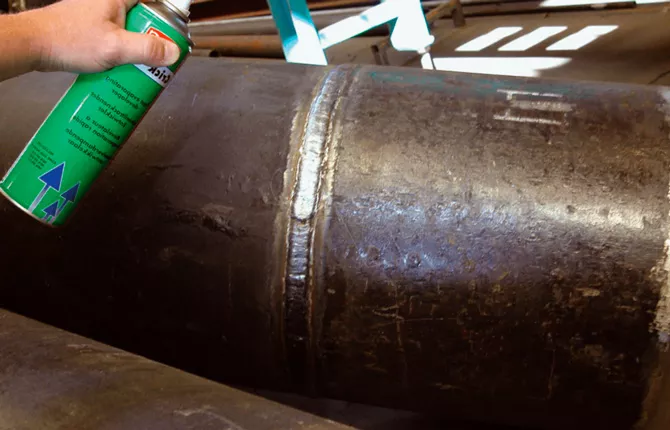
Las pruebas no destructivas de una tubería que no está sujeta a esfuerzos importantes se pueden realizar de formas más sencillas: hidráulicas o neumáticas. Para ello, se impulsa agua o aire a presión por el interior de la línea, respectivamente.
En el primer caso, los ensayos no destructivos se realizan detectando manchas del lado opuesto de la conexión, es decir, del exterior de las tuberías. En el segundo, se usa adicionalmente espuma, que se aplica a la soldadura. Si comienza a burbujear, hay un defecto.
Las pruebas no destructivas de tuberías han facilitado la verificación de la integridad y la calidad de las conexiones de las tuberías. El uso de la detección de fallas, especialmente rayos X y ultrasonidos, prácticamente ha acercado la probabilidad de detectar defectos de soldadura al 100%. Al mismo tiempo, dicho control le permite averiguar dónde se encuentra el defecto, cuántos de ellos, qué tamaños y formas.
¿Cree que es necesario aplicar métodos más sofisticados de ensayos no destructivos de tuberías, o puede ser suficiente el suministro de agua/aire al sistema? Escribe en los comentarios. Comparta el artículo en las redes sociales y márquelo como favorito.
Aprenderá más sobre cómo se prueban las soldaduras en el video.
Fuentes:
- https://iseptick.ru/truby-i-fitingi/nerazrushayushhij-kontrol-truboprovodov-i-svarnyx-soedinenij-metody-kontrolya.html
- https://elsvarkin.ru/texnologiya/kontrol/soedinenij-truboprovoda
- https://spark-welding.ru/montazh-i-remont/metody-nerazrushayushchego-kontrolya-truboprovodov.html