El aluminio y sus aleaciones se utilizan a menudo para crear diversas estructuras técnicas y tecnológicas. El aluminio puro no se usa tan ampliamente como sus aleaciones, debido a sus propiedades de baja resistencia y alta ductilidad. Cabe señalar que antes de soldar aluminio, es necesario tener en cuenta las peculiaridades del proceso de soldadura, debido a las propiedades físicas y químicas de este metal.
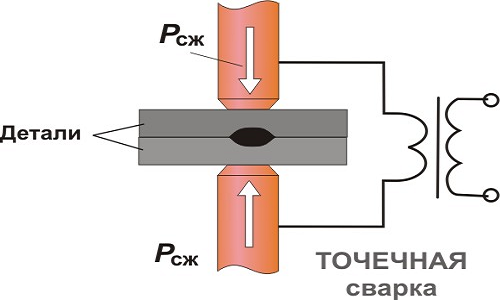
El esquema de tecnología de soldadura por puntos de aluminio.
El principal problema con la conexión del aluminio es la formación continua en la superficie de la película de óxido de metal soldado Al2O3, que es refractaria e interfiere con la fusión. Además, los óxidos de aluminio tienen un punto de fusión bastante alto (+ 2050 ° C) en comparación con el mismo indicador para el metal en sí (+ 658 ° C), que realiza sus propios ajustes en el proceso. El aluminio tiene una alta conductividad térmica, lo que implica el uso de técnicas y métodos especiales.
Tipos de soldadura de aluminio
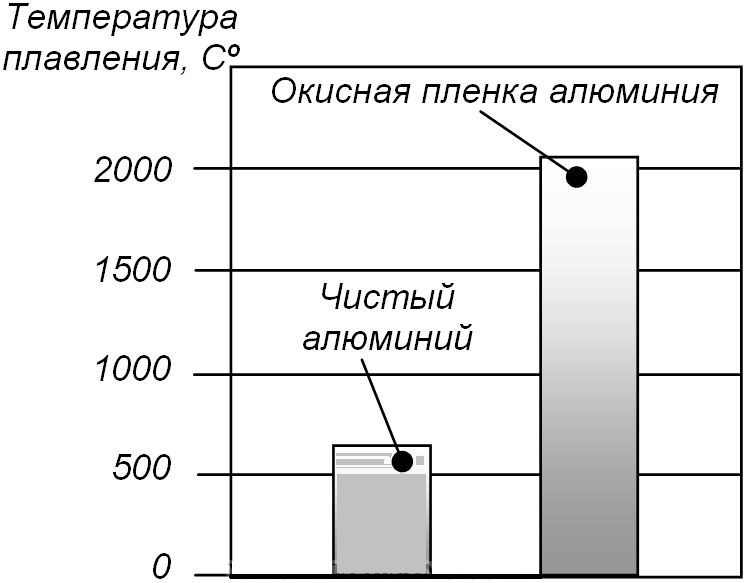
El punto de fusión del aluminio.
Puede soldar aluminio utilizando los siguientes tipos de soldadura:
- arco eléctrico (automático, manual);
- arco de argón (automático, semiautomático y manual);
- gas
Consideremos el método más común y efectivo de soldadura de aluminio: usar un electrodo manualmente con soldadura de arco de argón en corriente continua con polaridad inversa.
Soldadura al arco de argón
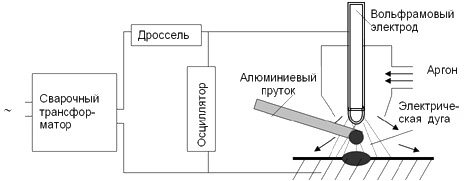
Esquema de soldadura al arco de argón de aluminio.
Las ventajas de este tipo son la falta de uso de materiales auxiliares (recubrimientos de electrodos, flujos). El proceso se realiza de forma manual, semiautomática y con métodos automáticos.
Se debe tener en cuenta que cualquier trabajo de soldadura debe llevarse a cabo solo en equipos reparables, en una habitación bien ventilada o en una habitación con suministro y ventilación por extracción y con el uso de equipo de protección personal (solapa, guantes de cuero, monos, zapatos de seguridad).
Materiales y herramientas para soldadura manual con arco de argón.
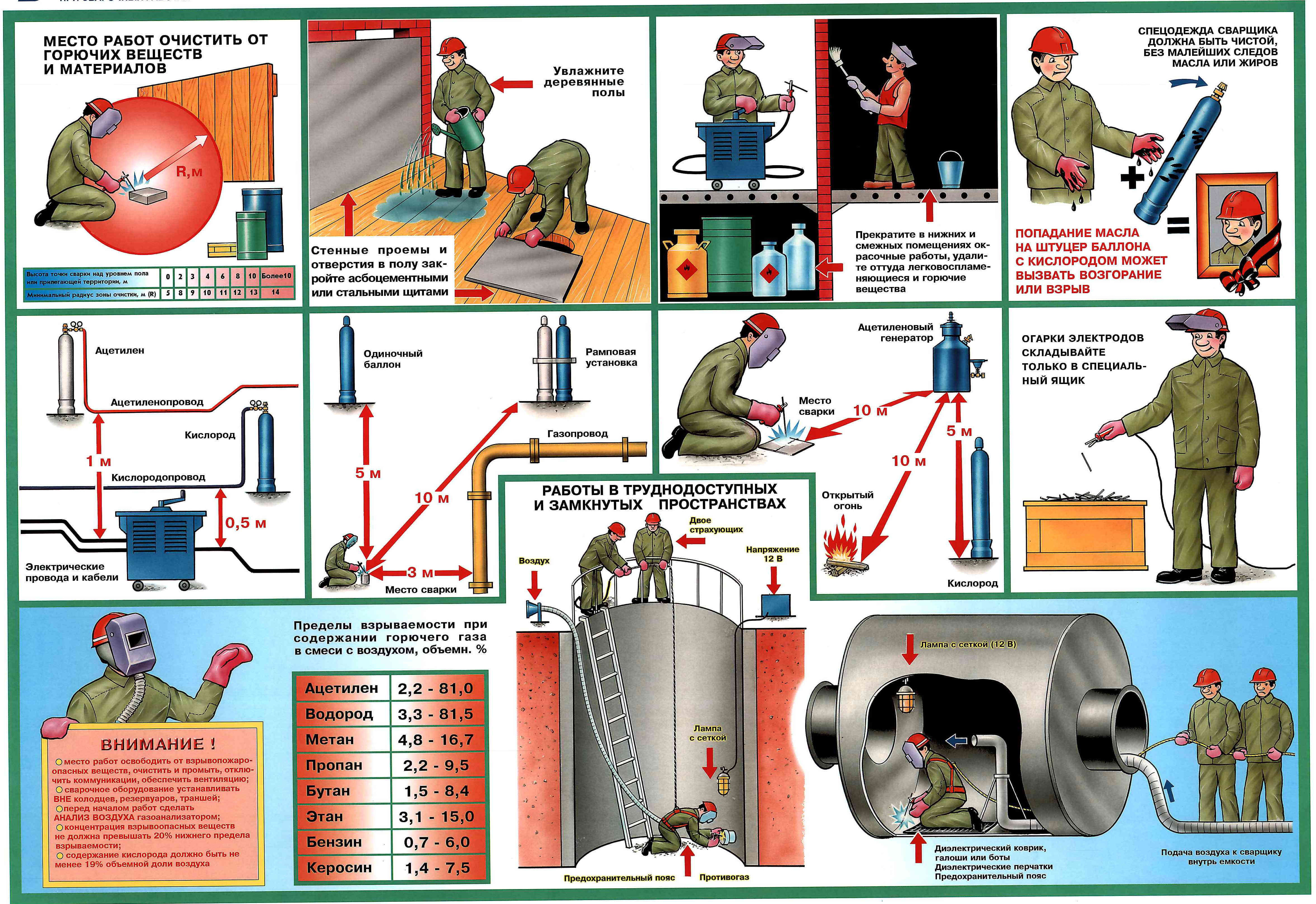
Seguridad durante la soldadura.
Para este tipo de compuesto de aluminio, un electrodo de tungsteno con corriente directa y polaridad inversa requerirá:
- solvente (acetona, gasolina);
- cepillo de metal;
- solución de grabado;
- ácido nítrico (solución);
- baño de preparación de metales;
- electrodos de tungsteno no consumibles;
- máquina de soldar o máquina de soldar para soldadura con arco de argón con un tipo específico de antorcha, electrodos de tungsteno, argón seco (pureza 99.8%), soportes de soldadura, alambre de relleno del diámetro requerido;
- revestimiento de acero inoxidable (cobre);
- Equipo de protección personal (escudo, guantes de cuero, guantes de goma), monos, zapatos de seguridad.
Preparación de metales antes de la soldadura.
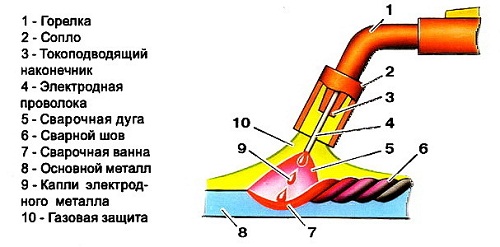
Esquema de un dispositivo semiautomático para soldadura de aluminio.
Antes de cocinar aluminio de cualquier tipo, las piezas de aluminio se someten a una preparación preliminar, que consiste en desengrasar la superficie del material y disolver la película de óxido.
El desengrase con metales se realiza tratando su superficie con solventes (acetona, gasolina, etc.). Después de eso, limpie los óxidos mecánicamente con un cepillo o mediante grabado químico con soluciones químicas (hidróxido de sodio - 45-55 g, fluoruro de sodio - 10-50 g, agua - 1 l). Luego, el aluminio se lava con agua pura durante 0, 5-1 minutos, luego la superficie del metal se neutraliza con ácido nítrico (solución de 25-30% durante 1-2 minutos), luego el metal se lava con agua corriente, luego con agua caliente, luego se seca el metal Hasta que esté completamente seco.
Dicha preparación se lleva a cabo no antes de 2 a 4 horas antes de la soldadura. De la misma forma se debe procesar alambre para aditivos en el caso de su aplicación.
Tecnología de aluminio compuesto
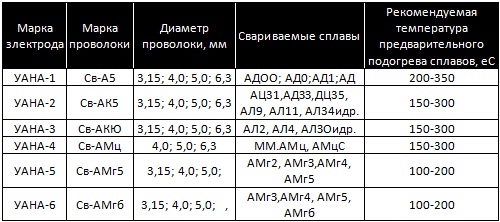
Las principales características de los electrodos revestidos para soldadura de aluminio.
Las planchas de aluminio con un espesor inferior a 5 mm se hierven sin separar los bordes. Con un espesor de aluminio de hasta 20-25 mm, se puede trabajar sin precalentar el material. Si las piezas tienen un grosor de más de 20 mm, entonces el material debe precalentarse a 300-400 ° C.
La soldadura con arco de argón se puede realizar en corriente alterna o directa (polaridad inversa). Cuando se trabaja con corriente alterna, se utilizan osciladores-estabilizadores del arco de soldadura. La soldadura de electrodos no consumibles se realiza en corriente continua con polaridad inversa y en corriente alterna, con o sin material aditivo. En el papel del alambre de relleno, use la marca de AK de la producción nacional según GOST 7878-75 o análogos extranjeros. Al soldar juntas en forma de T, angulares o de tope, es obligatorio el uso de material de relleno. En el caso de trabajos en bridas y topes con un pequeño espesor de aditivos de aluminio no se utilizan. Los parámetros (diámetro D) del aditivo de alambre para el trabajo manual se seleccionan según el grosor del aluminio (S):
- S hasta 2 mm, D aditivos hasta 1-1, 5;
- S = 2-5 mm, D aditivos = 1.5-3;
- S más de 5 mm, D aditivos = 3-4.
En la soldadura con arco de argón, los electrodos de tungsteno se utilizan con un espesor de 0, 8 a 8, 0 mm y el tungsteno lantano de producción nacional o extranjera. Su diámetro se elige según el tipo de corriente y los valores de su fuerza (I). Entonces, a una corriente constante con polaridad inversa:
- D electrodo = 1 mm, I a 10 A;
- D electrodo = 2 mm, I = 10-30 A;
- D electrodo = 3 mm, I = 20-40 A;
- D electrodo = 4 mm, I = 40-80 A;
- D electrodo = 5 mm, I = 60-100 A;
- D electrodo = 6 mm, I = 80-130 A.
El proceso de soldadura con arco de argón manual de elementos y estructuras de aluminio consta de varias etapas.
Realice este tipo de trabajo en un revestimiento de acero inoxidable o láminas de cobre. La elección del modo (corriente I, caudal de argón Q) de la soldadura al arco de argón con electrodos de tungsteno depende de la sección transversal de las piezas a soldar (S), la presencia de aditivos o bridas y tiene los siguientes parámetros:
- extremo a extremo con aditivo, S = 1, 0 mm, I = 65-85 A, Q = 4-5 l / min;
- extremo a extremo con un aditivo, S = 1.2, I = 70-90 A, Q = 5-6 l / min;
- extremo a extremo con aditivo, S = 1.5, I = 80-100 A, Q = 7-8 l / min;
- extremo a extremo con un aditivo, S = 2.0, I = 90-110 A, Q = 7-8 l / min;
- extremo a extremo con aditivo, S = 3.0, I = 100-120 A, Q = 8-9 l / min;
- sin añadir a tope, S = 0, 8 mm, I = 45-55 A, Q = 4-5 l / min;
- sin aditivo trasero, S = 1.0, I = 50-65 A, Q = 4-5 l / min;
- sin aditivo trasero, S = 1.2, I = 60-70 A, Q = 5-6 l / min;
- sin adición a tope, S = 1.5, I = 70-90 A, Q = 7-8 l / min;
- sin aditivo trasero, S = 2.0, I = 90-110 A, Q = 7-8 l / min;
- sin aditivo trasero, S = 3.0, I = 100-120 A, Q = 8-9 l / min;
- quemado, S = 0, 8 mm, I = 40-45 A, Q = 4-5 l / min;
- bengala, S = 1.0, I = 45-55 A, Q = 4-5 l / min;
- flanging, S = 1.2, I = 55-70 A, Q = 5-6 l / min;
- flanging, S = 1.5, I = 70-85 A, Q = 7-8 l / min.
Para la soldadura de arco de argón manual con electrodo no consumible, se utilizan unidades domésticas especiales como UDAR, UDG o sus análogos extraños.
El proceso de conexión argón-arco de las piezas comienza manualmente con la excitación (ignición) del arco. Antes de esto, active el suministro de argón y establezca el amperaje apropiado de acuerdo con el modo seleccionado. El arco se enciende de las siguientes maneras: golpeando el electrodo en la superficie de aluminio y tocando el electrodo perpendicular en el punto de origen. Si se produce una ruptura del arco, se hace otro encendido antes del cráter en el aluminio soldado, y luego se devuelve al material ya depositado para traer la contaminación del cráter a la superficie. Además, el trabajo se lleva a cabo en la dirección deseada. Cabe destacar que al realizar soldadura manual con arco de argón, no es necesario realizar movimientos oscilatorios con antorcha, ya que Posible violación de la protección de la zona de soldadura. El ángulo entre el plano del producto y el eje del quemador debe ser de 75 a 80 °. Y el ángulo entre el producto y el alambre de relleno con su uso - 15-20 °. El quemador debe moverse después de la barra de relleno.
La ubicación de la costura en el espacio determina la ubicación del electrodo. Mueva el electrodo "lejos de usted" o "hacia usted mismo". De acuerdo a la trayectoria de su movimiento se reciben costuras medianas o estrechas. El tipo de movimiento del electrodo determina el calentamiento o no calentamiento de los bordes metálicos.
Las costuras son medianas (de 350 a 1000 mm), largas (más de 1000 mm) y cortas (de 250 a 300 mm). Las costuras largas se hierven en piezas de 250-300 mm. Dependiendo del grosor de las piezas, las costuras pueden ser de una sola capa (una sola pasada) y de múltiples capas (múltiples pasadas). Las costuras de una sola capa son económicas y rápidas de realizar, pero el metal de sutura tiene una ductilidad insuficiente. En el caso de una soldadura multicapa, el metal soldado tiene buenas propiedades mecánicas. Al realizar trabajos multicapa para aluminio con un grosor de más de 20–25 mm, la primera capa principal debe realizarse cualitativamente, lo que determina las propiedades de resistencia de toda la soldadura.
Una vez que se han completado las costuras, el flujo de argón se apaga y las costuras se someten a un procesamiento adicional; los residuos de escoria se eliminan de la superficie de la costura, ya que La escoria tiende a corroer el metal. La eliminación de la escoria se lleva a cabo lavando la costura en agua caliente.
Cabe señalar que es posible cocinar aluminio con un electrodo no solo con soldadura de arco de argón manual, sino también con soldadura de arco manual, así como con soldadura de arco automática. Sin embargo, estos tipos de soldadura de piezas de aluminio no se usan ampliamente debido al uso de fundentes, así como debido a una serie de características de los electrodos utilizados y la mala calidad de las costuras. Con la soldadura automática de arco de argón y la soldadura semiautomática de arco de argón, la alta calidad de las soldaduras se conserva sin la necesidad de utilizar flujos. El tipo de compuesto de aluminio más ineficiente es la soldadura con gas utilizando sopletes y antorchas de gas.