Antes de comenzar el proceso de soldadura de acero inoxidable, es necesario explorar todas las características posibles de dicha soldadura. Hervir acero inoxidable: no es el ejercicio más fácil, cuya complejidad depende de muchos matices.
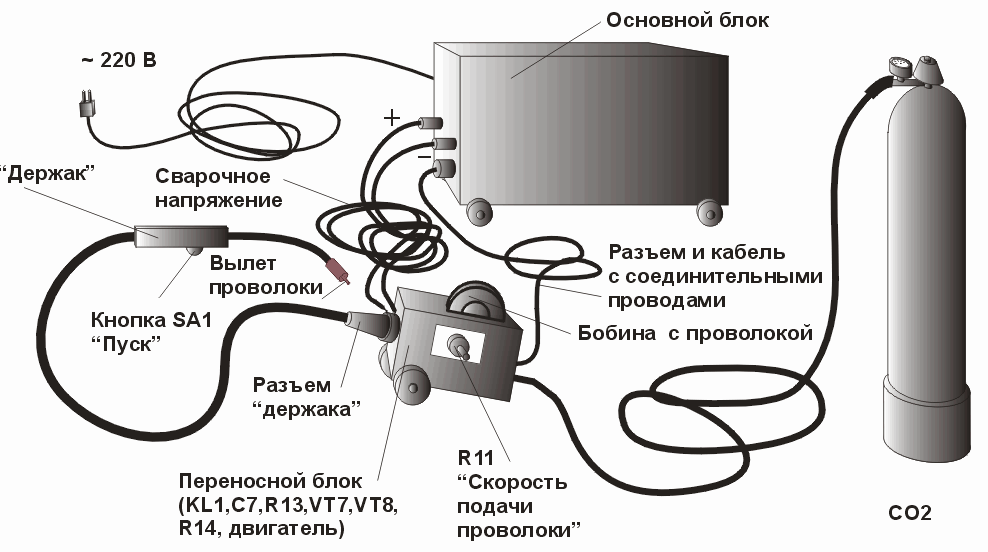
Esquema de soldadura de dispositivo semiautomático.
Características principales que necesariamente pueden afectar la calidad de la soldadura:
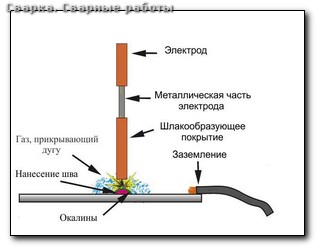
Soldadura de acero inoxidable semiautomática.
- Expansión lineal y retracción por colada. Si la contracción es alta, entonces aumenta la posibilidad de deformación del metal durante el trabajo con electrodos de soldadura y luego aumenta. Y si las piezas a soldar son lo suficientemente amplias y no hay espacio entre ellas, entonces aumenta la posibilidad de grandes grietas.
- Conductividad térmica: en el acero inoxidable, se reduce casi a la mitad en comparación con otros metales, por lo que al soldarlo, es necesario reducir el amperaje en un 15-20%.
- La resistencia eléctrica es bastante alta, por lo que la soldadura con electrodos convencionales es imposible debido a su calentamiento excesivo. Por lo tanto, los electrodos especiales se fabrican sobre la base de varillas de níquel-cromo, con una longitud máxima de 3, 5 cm para la soldadura de acero inoxidable.
- Corrosión intergranular: el acero inoxidable es inherente a la capacidad de perder propiedades anticorrosivas, si el modo térmico de soldadura es incorrecto o si se selecciona la máquina incorrecta. La esencia de este proceso es que cuando la temperatura alcanza más de 500 grados centígrados, el carburo de cromo y hierro aparece en el borde del metal, lo que conduce a la corrosión del metal. Sin embargo, existen métodos para combatir esto, por ejemplo, el enfriamiento rápido en una variedad de formas.
Características de la soldadura de acero inoxidable.
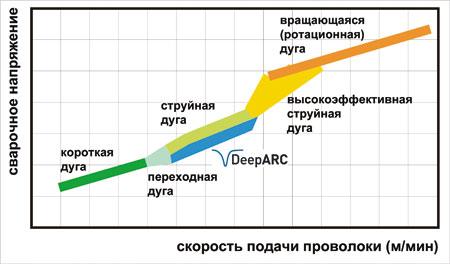
Doble pulso para soldadura perfecta de aluminio y acero inoxidable.
Para soldar correctamente y con precisión el acero inoxidable, también es necesario tener en cuenta el hecho de que algunas de sus propiedades físicas difieren del acero común:
- resistividad eléctrica - 6 veces mayor;
- punto de fusión - por debajo de 100 grados centígrados;
- Conductividad térmica - menos por 2/3;
- La expansión térmica es la mitad de alta.
Existen métodos completamente diferentes para soldar su propio acero. Por ejemplo, la soldadura por arco con electrodos especiales de tungsteno, que se lleva a cabo en un ambiente inerte, se utiliza si el espesor del metal es superior a 1, 5 mm. Si es necesario soldar acero fino o tuberías, es mejor recurrir a la soldadura con la ayuda de electrodos de fusión en gas inerte.
La soldadura por arco pulsado debe ser aplicable solo a las láminas de acero cuyo grosor es de 0.8 mm. Con un arco corto que utiliza electrodos de fusión, el acero con un espesor de 0, 8 a 3, 0 mm se utiliza para soldar, y el acero con un espesor de lámina de más de 3, 0 mm se utiliza para la transferencia de chorro de metal.
Sin embargo, si se considera la soldadura con plasma, se puede concluir que es adecuado para una variación muy amplia en el espesor, por lo tanto, se usa mucho más a menudo. La soldadura por arco sumergido se utiliza para espesores de metal superiores a 10 mm. Pero los métodos de soldadura más populares son la soldadura con electrodos recubiertos, los electrodos de tungsteno en un entorno de argón y la soldadura semiautomática de argón con alambre de acero inoxidable.
Soldadura con electrodos revestidos.
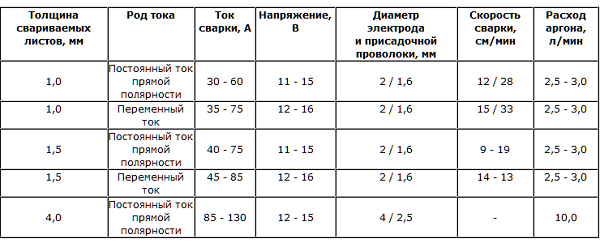
Modos de soldadura en gases inertes.
Si no le importa qué tipo de electrodos para conducir la soldadura y usted no tiene ningún requisito especial para la junta de soldadura, entonces la forma más aceptable será soldar con electrodos recubiertos (estos incluyen los electrodos OZL-8, NIAT-1, TsL-11). De todos los electrodos, es mejor elegir aquellos que proporcionarán, después de la soldadura, resistencia a la corrosión, resistencia al calor y buenas propiedades mecánicas.
La soldadura debe realizarse a una corriente constante con polaridad inversa obligatoria. Se debe tener cuidado para asegurar que la costura se derrita al mínimo, ya que los electrodos utilizados para soldar acero inoxidable tienen un diámetro pequeño y necesitan un mínimo de energía térmica. La fuerza de la corriente en el proceso de soldadura de acero inoxidable debe ajustarse estrictamente a un 15-20% más bajo que cuando se suelda metal común. Con alta corriente debido a la baja conductividad térmica y con alta resistencia de los electrodos revestidos, puede ocurrir un sobrecalentamiento significativo e incluso un desprendimiento de las piezas. Debido a esto, tales electrodos tienen una alta tasa de fusión, por lo que si los usa por primera vez, al principio puede ser inusual.
Para preservar las características de corrosión de la soldadura, el enfriamiento acelerado debe organizarse durante la soldadura. Para ello puede utilizar juntas de cobre o un determinado soplado de aire. Si el acero es cromo-níquel, puedes enfriarlo con agua.
Soldadura de acero inoxidable mediante electrodos de tungsteno.
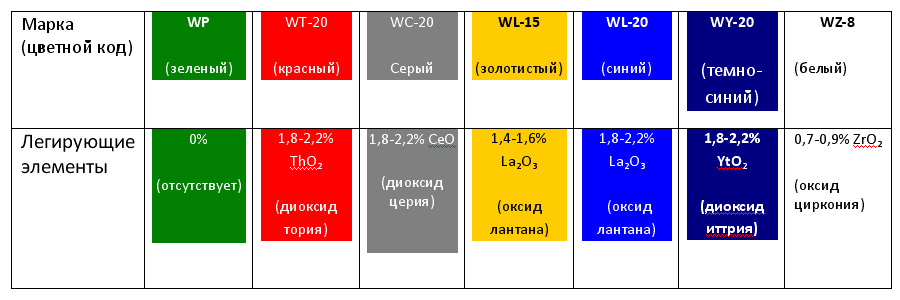
Electrodos de tungsteno.
La soldadura con electrodos de tungsteno en un entorno inerte es adecuada cuando el metal a soldar es muy delgado o si los requisitos de calidad de la unión soldada son muy altos. Por ejemplo, si necesita cocinar tuberías que luego se utilizarán para transportar gases o líquidos a alta presión, este método de soldadura es ideal. El procedimiento se lleva a cabo en un entorno de argón, la corriente puede ser constante y variable, pero de polaridad directa. En el papel del material de relleno se recomienda tomar el alambre con un mayor nivel de dopaje que el metal. Durante la operación, deben evitarse los movimientos oscilatorios con electrodos para evitar perturbar la zona de cocción, lo que puede provocar la oxidación de la soldadura y aumentar el costo del proceso en sí.
En el reverso del aire, la costura debe protegerse soplando argón, pero aún el acero inoxidable no es muy crítico para tal protección, pero es necesario eliminar incluso la más mínima posibilidad de que las partículas de tungsteno entren en el baño de soldadura de todos modos. En este caso, la ignición sin contacto del arco de soldadura ayudará, también puede usar una placa de carbón o grafito para el mismo propósito.
Una vez finalizado el trabajo, para no abusar del electrodo de tungsteno, el gas no debe apagarse inmediatamente, sino después de un tiempo (generalmente de 10 a 15 segundos). Esto ayuda a evitar la fuerte oxidación de los electrodos calentados, lo que aumenta su vida útil.
Prevención de defectos
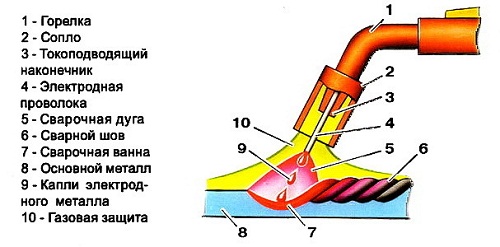
Soldadura de acero inoxidable con sus propias manos.
Al soldar acero inoxidable, siempre es necesario tener en cuenta todas sus características; de lo contrario, después del trabajo, pueden ocurrir varios defectos de soldadura indeseables, por ejemplo, la formación de corrosión de “cuchillas”. Las grietas calientes pueden ocurrir debido a las altas temperaturas, principalmente debido a la fragilidad de las costuras.
Para evitar este tipo de incidentes, es mejor utilizar materiales de relleno que ayuden a crear costuras fuertes. Sin embargo, tales materiales no deben contener ferrita más del 2%. Además, la soldadura por arco también ayudará a reforzar las costuras, en las que la longitud del arco será pequeña. Debe recordarse que los cráteres en el metal base no deben mostrarse.
Si usa soldadura automática, debe recordar que generalmente se usa para cocinar a velocidades más bajas. Pero para reducir el riesgo de deformación, es mejor hacer menos enfoques, porque la soldadura a la velocidad máxima contribuye a una mejor resistencia a la corrosión.
Por lo tanto, antes de elegir qué electrodos soldar un acero inoxidable, debe familiarizarse con todas sus características y características, saber exactamente qué requisitos se colocarán en la costura de soldadura y para qué fines se utilizará el producto.