Cada soldador sabe que las estructuras soldadas tienen propiedades operativas que están determinadas por la calidad de las soldaduras.
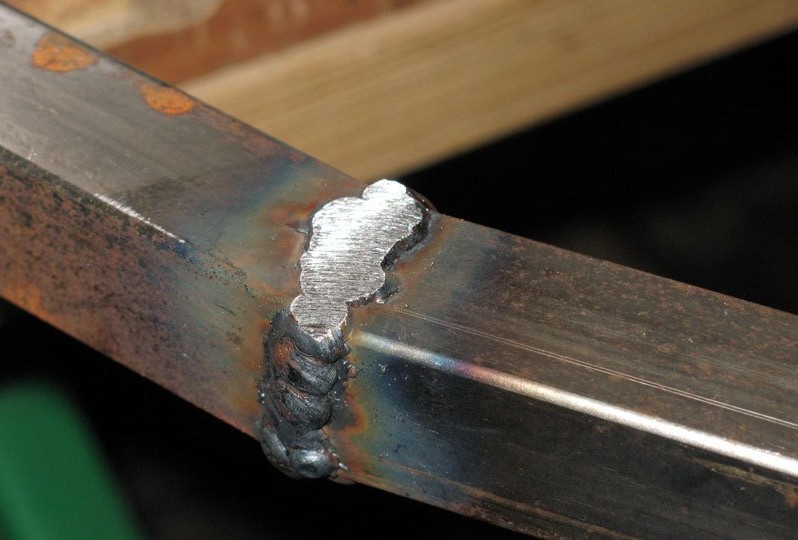
Para obtener una construcción confiable y duradera, es necesario hacer una costura de alta calidad.
La calidad inadecuada de la costura de la soldadura causa una rápida destrucción de las soldaduras, y si la densidad es insuficiente, su estanqueidad se verá afectada. El proceso de destrucción se acelera cuando se utiliza la estructura en condiciones de alta presión.
El propósito de la inspección de soldadura.
Antes de enviar un producto terminado soldado a una inspección posterior, es necesario controlar el nivel de calidad de sus soldaduras, y esto ayuda a identificar no solo los defectos externos, sino también los ocultos, para eliminarlos. La construcción soldada se aplica solo después de un control cuidadoso.

Después de la soldadura, debe inspeccionar cuidadosamente la costura para detectar grietas e incompetencia.
En la primera etapa, el producto se somete a un examen externo e identifica diversos defectos en las soldaduras, incluida la presencia de grietas y la falta de penetración. La detección de estos defectos también está disponible a simple vista, y los tipos de deficiencias restantes se determinan mediante el uso de equipos especiales.
Existen soldaduras de control, que se clasifican como destructivas y no destructivas. Los últimos tipos incluyen no solo un método de examen externo, sino también los siguientes tipos de control de costura:
- Capilar
- Ultrasonido
- La radiacion
- Magnético
- Permeabilidad.
El uso de métodos de control no destructivos no está asociado con un cambio en la apariencia del producto en sí. Se utilizan métodos destructivos cuando se verifica la liberación de piezas soldadas en cantidades suficientes utilizando un tipo constante de soldadura y las mismas condiciones.
Inspección y ensayo de soldaduras: métodos de inspección.
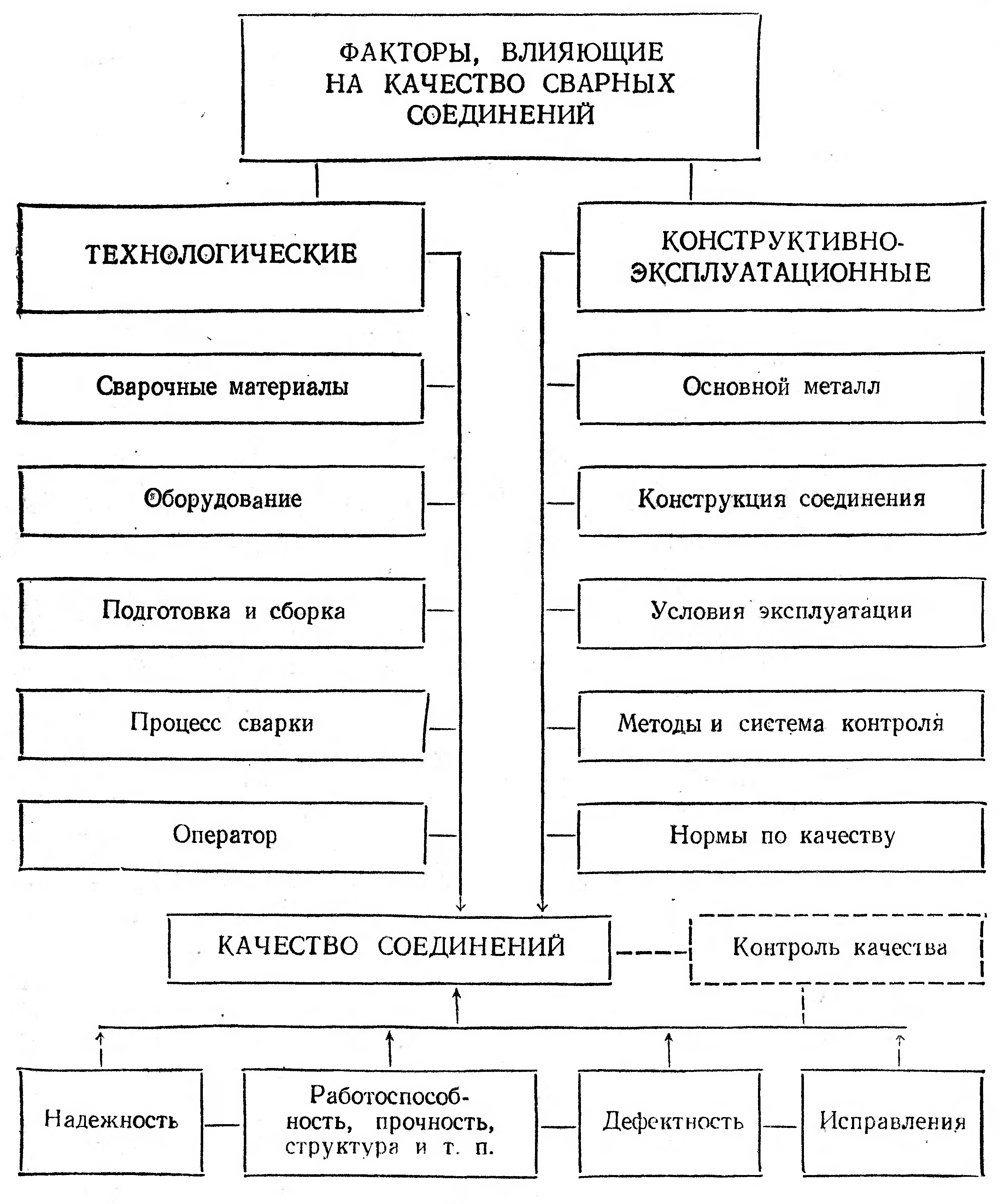
Factores que afectan la calidad de las soldaduras.
Las soldaduras se pueden controlar de varias maneras, para lo cual se proporciona su clasificación, lo que incluye los siguientes métodos utilizados en la inspección:
- Química
- Mecánica
- Fisico
- Examen externo
Si consideramos cada uno de ellos en detalle, entonces uno de los más comunes y accesibles es un examen externo, que no está asociado con ningún costo de material. El uso de cualquier unión soldada está sujeto a este método de control, independientemente del proceso de operaciones posteriores, seguido de otros métodos de control de las juntas.
Puede realizar un examen externo con la identificación de casi todos los tipos de defectos en las soldaduras. Este método de control está asociado con la identificación de penetración deficiente, socavaduras, flacidez u otros defectos que están disponibles para su visualización. Para la implementación del examen externo se puede aplicar lupa, que aumenta 10 veces.
Bajo las condiciones del examen externo, la observación puede ser no solo visual, sino también relacionada con la medición de la soldadura, realizando mediciones de los bordes que se preparan con anticipación. El proceso de producción en masa de productos soldados se asocia con el uso de plantillas especiales que le permiten realizar mediciones de cada parámetro de la soldadura con la mayor precisión posible.
Metodos de control fisico
La aplicación del método magnético de soldadura de costuras.
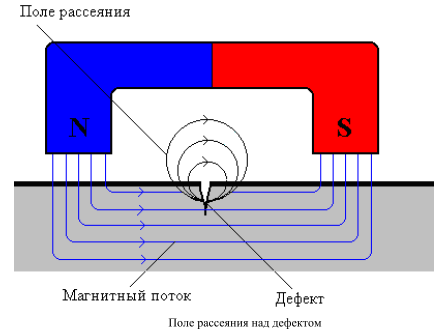
Esquema del método magnético de control de calidad de la soldadura.
La detección de defectos en el proceso de control magnético se basa en la capacidad del campo magnético para dispersarlo. Para este propósito, es necesario conectar el núcleo electromagnético y luego colocarlo en el solenoide. El compuesto magnetizado debe tener una superficie, recubierto previamente con limaduras de hierro, escamas, etc. Se deben usar elementos que reaccionen ante la aparición de campos magnéticos.
Si la soldadura tiene defectos, se produce la formación de agrupaciones de polvo que, al interactuar con un campo magnético, comienza a moverse con la formación de un espectro direccional magnético. Para facilitar el movimiento del polvo bajo la influencia de los campos magnéticos, los productos soldados golpean, lo que le da la mayor movilidad a los granos pequeños y pequeños.
La fijación del campo magnético de dispersión se realiza mediante un dispositivo especial, es decir, un detector de fallas magnetográfico. Para determinar la calidad de la conexión, puede utilizar el método de comparación con el estándar. Este método es simple y confiable, así como barato. El método de control magnético de las costuras de soldadura es indispensable en el proceso de tendido de tuberías, que desempeñan un papel responsable. Se utiliza a menudo durante la construcción.
Método de control de radiación y método de ultrasonido.
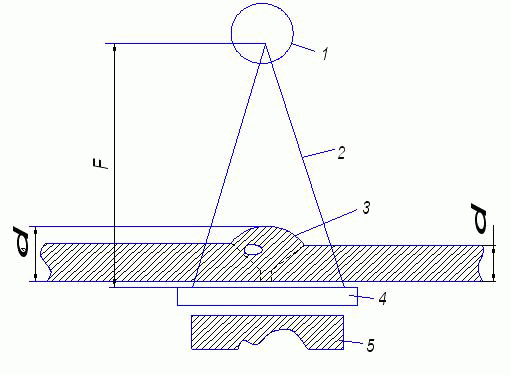
Esquema de control radiográfico: 1 - fuente de radiación; 2 - paquete recto; 3 - soldadura; 4 - cassette con detector y pantallas; 5 - gráfico de intensidad de radiación.
El método de control de radiación está asociado con la determinación de defectos en cualquier cavidad de las soldaduras que son invisibles. Costuras translúcidas con rayos X o con radiación gamma, que pueden penetrar en la estructura metálica del producto.
La radiación es creada por fuentes especiales, rayos X o instalaciones basadas en gamma. La costura y la fuente de radiación deben estar una frente a la otra. La disposición de la película de rayos X está conectada con su instalación en un casete especial, que es opaco. Cuando la película se irradia con rayos X que pasan a través de la estructura metálica, quedan puntos que son más oscuros. Esto se debe a la menor absorción de rayos por lugares defectuosos.
El uso del método de rayos X es seguro para la salud humana, pero la fuente de radiación, es decir, la máquina de rayos X, es demasiado incómoda. Úsalo exclusivamente en el hospital. La intensidad de la fuente de radiación gamma es significativa, lo que le permite controlar las soldaduras, que se caracterizan por el mayor grosor. El equipo portátil y la disponibilidad de métodos baratos hacen que este tipo de control sea el más común en la construcción.
La radiación gamma es más peligrosa que los rayos X, debido al paso de entrenamiento especial. El uso del método de control radiográfico tiene la desventaja de no poder detectar la presencia de grietas que no están ubicadas de acuerdo con la dirección del flujo de rayos.
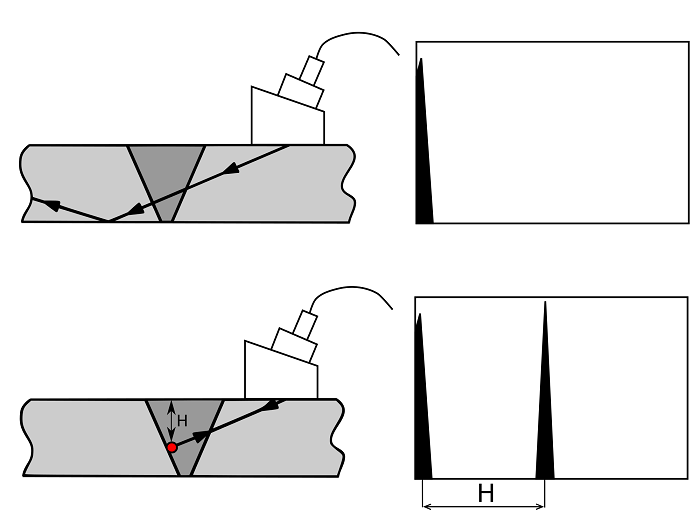
Inspección ultrasónica de soldaduras.
El uso de un método ultrasónico está asociado con el uso de un método de control acústico. Esto le permite identificar varias deficiencias, es decir, poros de gas y grietas, incluidos dichos defectos, por lo que no se utiliza el método de detección de fallas de radiación.
El método ultrasónico realiza pruebas relacionadas con la reflexión de ondas de sonido desde el límite de la separación de medios. El uso del método piezoeléctrico para crear una onda de sonido se ha generalizado como un método para controlar una soldadura. La base de este método es el principio de crear una oscilación mecánica como resultado de la imposición de un campo eléctrico alternativo.
Inspección de inspección destructiva
Condiciones para el método de control mecánico.
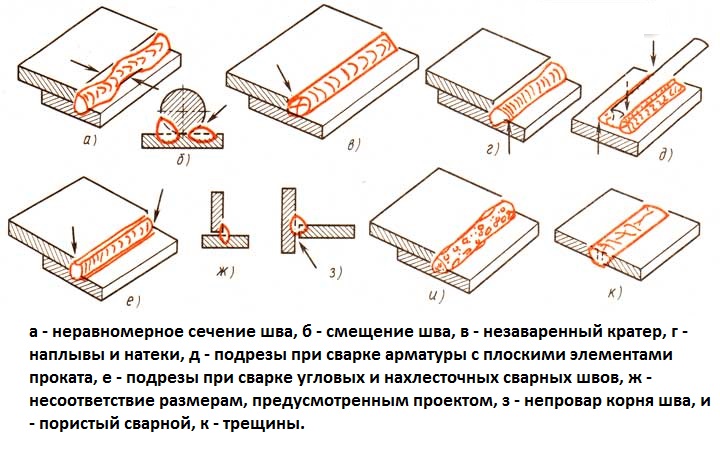
Patrón de defectos de soldadura.
La destrucción mecánica de productos en el proceso de prueba por el método metalográfico es necesaria para identificar las características de las soldaduras.
El objeto de las pruebas son muestras con costuras soldadas, que se cortan de las costuras de las muestras de control especialmente soldadas de las uniones. Son muestras realizadas en base a los requisitos relevantes para el nivel tecnológico de productos de soldadura en condiciones especiales. Se requiere tomar las muestras que tengan la forma correspondiente y un tamaño determinado.
El objetivo principal de los controles de control es el análisis y evaluación:
- fuerza de la soldadura;
- calidad del metal;
- elección correcta de la tecnología;
- Nivel de cualificación del trabajador-soldador.
Puede comparar las características de las soldaduras con las propiedades del metal. En caso de resultados insatisfactorios, no se anota la correspondencia de los totales para el nivel dado. Las pruebas mecánicas se llevan a cabo sobre la base de GOST 6996-66, donde los tipos relevantes de pruebas de control de uniones metálicas soldadas para:
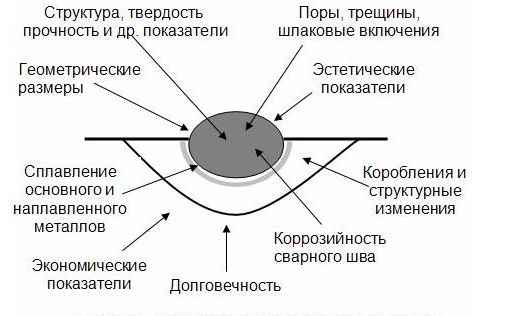
Parámetros para el control de calidad de la soldadura.
- Varias secciones individuales y en general.
- Asunto estático estiramiento y flexión.
- La naturaleza del choque de flexión.
- El nivel de resistencia en condiciones de envejecimiento.
- El resultado de medir las características de la dureza.
Realización de pruebas de control para identificar el estiramiento estadístico asociado con la determinación del nivel de resistencia de la soldadura. La definición de flexión estadística implica el estudio de las propiedades de plasticidad de la soldadura. Las pruebas asociadas con la detección de defectos se llevan a cabo antes de la formación de las primeras deficiencias en el área de la zona estirada, teniendo en cuenta el ángulo de flexión.
Pruebas para identificar la flexión estadística producida utilizando muestras tecnológicas tomadas de nodos con costura transversal o longitudinal. Al realizar pruebas de flexión y rotura por impacto, se determina la resistencia al impacto de la soldadura. Según su dureza revelada, se examinan cada uno de los cambios estructurales del metal, los valores de su grado de perforación después de la soldadura y durante el enfriamiento posterior.
Aplicación de métodos de control macro y microestructural.
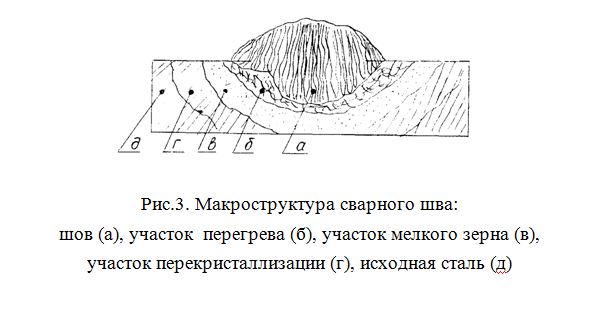
Diagrama de la microestructura de la soldadura.
El estudio de los metales, que se realiza sobre la base del método macro y microestructural, incluye no solo el proceso de detección de la presencia de defectos de cierta naturaleza, sino también la determinación de la calidad de la unión soldada.
El método macroestructural implica el estudio de las macrosecciones que están presentes en las fracturas metálicas, que se determinan con una lupa o una inspección visual. Los estudios macro determinan la naturaleza de cada defecto, su ubicación, si son visibles en diferentes zonas de las soldaduras.
El análisis microestructural está asociado con el análisis de la estructura de los metales. En el proceso de investigación, es posible un aumento visual de 50-2000 veces si se utiliza un microscopio óptico. El microscaneado se asocia con la determinación de la cantidad de metal, la detección de quemaduras, la presencia de óxidos en su estructura, la contaminación de las soldaduras, la presencia de inclusiones no metálicas. Esto hace posible estudiar los granos de metal, determinando su tamaño, para investigar los cambios en la composición del metal. Posible detección de poros microscópicos, grietas, otros defectos que llenan las soldaduras.
El uso de métodos apropiados para producir secciones delgadas en estudios metalográficos está asociado con la preparación de muestras para el control al eliminarlas del producto principal. La realización de análisis metalográficos está asociada con el uso adicional de métodos químicos.
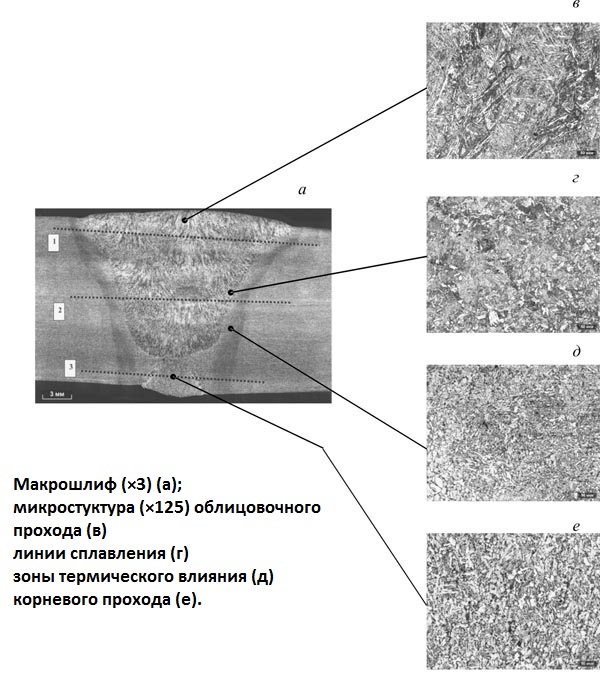
Estudios metalográficos de la soldadura.
Las pruebas permiten obtener las características correspondientes de las soldaduras, que tienen en cuenta las condiciones apropiadas para el uso de estructuras metálicas soldadas. El proceso de control está asociado con la identificación de la resistencia a la corrosión de los productos que operan en entornos agresivos.
Todos los métodos de control relevantes se aplican en el proceso de destrucción de estructuras. El curso de estas pruebas se basa en la capacidad de la estructura para soportar una carga de diseño dada y la determinación de cargas destructivas con un cierto margen de seguridad.
Realizando pruebas de estructuras destructibles, monitorear el estado del esquema de destrucción, que debe ser comparado con las condiciones de operación de la estructura. El número de productos a probar debe cumplir con las especificaciones establecidas, que están determinadas por la organización existente del proceso de producción.
Método de ensayo no destructivo de soldaduras.
El control, que no es destructivo, está asociado no solo con la realización de un examen externo, incluido el estudio de la estrechez de las costuras. Le permite detectar defectos en la superficie, que pueden ser internos y ocultos.
La medición asociada con la realización de una inspección externa de la soldadura puede considerarse común debido a su simplicidad. La aceptación de cualquier unidad terminada soldada se lleva a cabo después de las primeras operaciones de control.
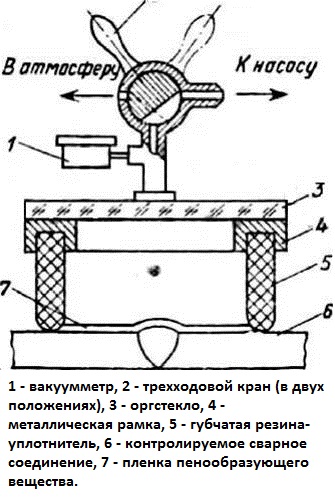
Control de circuito de fugas con una cámara de vacío.
El control de productos y ensamblajes se realiza cuando ya están completamente preparados.
Si un examen externo muestra que hay algún defecto, debe ser reparado antes de que comience la prueba. El control de la estanqueidad de las soldaduras se realiza mediante métodos tales como:
- Capilar (queroseno).
- Quimicos (amoniaco).
- Burbuja (hidráulica o presión de aire).
- Pasar la aspiradora
Detengámonos en estos métodos de control.
Investigación capilar
El uso del método capilar se basa en una cierta propiedad de los líquidos asociada con la posibilidad de penetración a través de los capilares, que son grietas microscópicas, en la estructura de los metales. El método capilar está asociado con la actividad del fluido en los capilares. El líquido es capaz de retraerse al penetrar los capilares. El uso de algunos de ellos (keroseno) le permite detectar la presencia de defectos en las soldaduras.
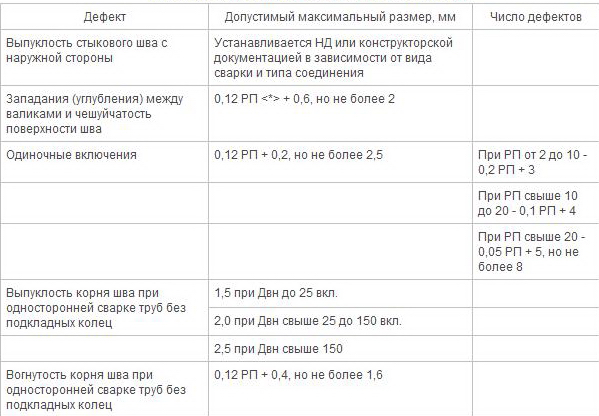
Mesa para inspección capilar de soldaduras.
El uso del control capilar está asociado con la inspección de cualquier producto soldado sin tener en cuenta sus formas, tamaños y materiales de los que están hechos. Este método es más adecuado para detectar varios defectos en la superficie de las costuras. Los defectos son invisibles, por lo que no pueden detectarse a simple vista, así como con una lupa.
Para probar las soldaduras de densidad basadas en el método capilar, se permiten sustancias especiales, que se llaman penetrantes. Al entrar en la estructura de los materiales investigados con defectos en la superficie de la unión soldada, los pintan en un color brillante, lo que le permite ver rápidamente la grieta.
Con un alto nivel de humectabilidad del líquido y el radio más pequeño del capilar, aumenta la profundidad y la velocidad de penetración del líquido. Como resultado de la aplicación del método capilar, es posible detectar no solo defectos invisibles o poco visibles con una cavidad abierta. Sin embargo, este método le permite identificar y tipos de defectos de extremo a extremo, si en el proceso de su detección utilizan queroseno.
Control químico y su aplicación.
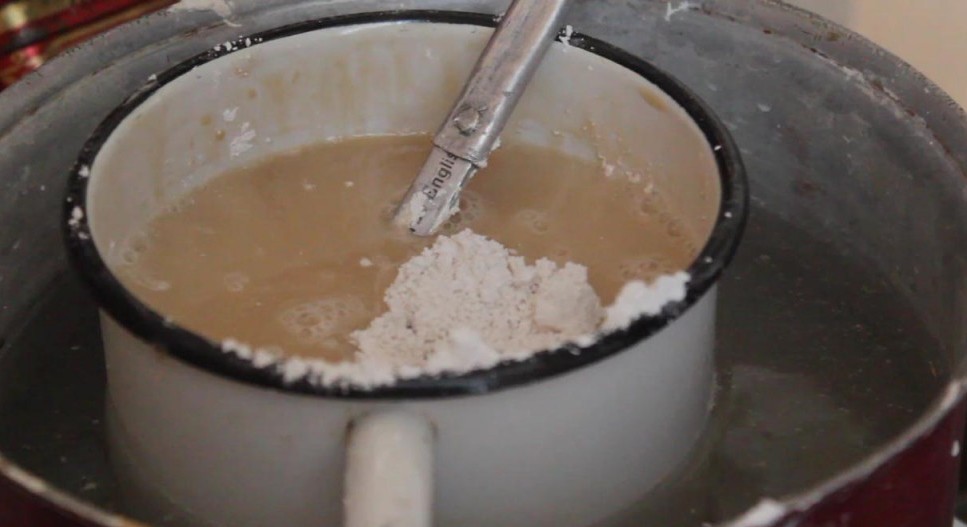
Para controlar la calidad de las soldaduras utilizando un método químico, se utiliza una solución de tiza en agua.
Para cubrir las soldaduras, se utiliza una solución de tiza en el agua que se utiliza para tratar el lado accesible de la soldadura, lo que permite una inspección e identificación exhaustiva de todos los defectos. Después de secar la superficie pintada, la costura debe humedecerse abundantemente con queroseno. Si las costuras están sueltas, esto se revela cuando hay una capa de tiza y rastros de queroseno en ella.
El control del amoníaco se realiza en presencia de indicadores que pueden cambiar su color en presencia de un medio alcalino que lo afecta. El reactivo en este proceso es el gas amoníaco, que se utiliza para el control.
Realización de pruebas, en un lado de la cinta de la pila de costuras de papel, que se humedece en una solución al 5% de un indicador especial. En el lado opuesto de la costura, el compuesto se trata con una mezcla de gas amoniaco y aire. Cuando el amoníaco penetra a través de uniones soldadas sueltas, se tiñe en presencia de defectos.
Métodos de control de presión hidráulica y de aire.
El control de la presión del aire se lleva a cabo cuando se verifica sobre la base del análisis de la estanqueidad de las uniones soldadas. Para ello, se sumergen completamente en un baño lleno de agua. A continuación, se suministra con aire comprimido, teniendo en cuenta el nivel de presión, que supera el trabajo en un 10-20%.
Si las estructuras son grandes, se cubren con indicadores de espuma después de que se haya aplicado la presión interna a la soldadura. Una solución de jabón puede actuar como un indicador de espuma. Si hay varias fugas en las soldaduras, comienzan a aparecer burbujas de aire. Las pruebas con aire comprimido o gas deben ir acompañadas del cumplimiento de las normas de seguridad requeridas.
La resistencia y la densidad de los productos se verifican mediante monitoreo en presencia de presión hidráulica. Las costuras están completamente selladas con tapones a prueba de agua. El secado de las juntas de aire se realiza mediante soplado de aire. Después de eso, el producto debe llenarse con una presión excesiva con agua, que es 1.5–2 veces más alta que el nivel de presión de trabajo. Además es necesario mantener el período requerido. Donde se produce una fuga, se pueden detectar defectos.
El control de vacío implica probar una soldadura que no se puede probar con queroseno, agua o aire. En el proceso de prueba, la costura se registra para la penetración de aire a través de las deficiencias de la soldadura. El registro se realiza en la misma área de costura en el mismo lado del producto donde se crea el vacío.